Our references & success
OUR REFERENCES
The majority of our customers are internationally renowned plastic convertors supplying the instructing parties & end users in the cosmetic, pharmaceutical, health & hair care, FMCG and food industries.We feel extremely proud to have been serving them for many years now, and will continue to do so with the same determination and spirit of innovation for many years to come!
Our long experience in manufacturing molds for products such as mascara, lip gloss, roll-ons and thick wall wide neck jars and tubs has been one of the keys to taking our customers on time to exactly where they wanted to go...Let us take you too!
SUCCESS STORIES
ADOP France is only satisfied at the completion of a project when our customer expresses his complete satisfaction.However, and moreover, from time to time packaging products receive prizes or awards…
This goes beyond ADOP’s wildest dreams, and we take pride in having contributed towards our customer’s success!
This mascara bottle in both PP & PA with its curved form & curved cores required precision calculations and engineering to ensure a balanced wall repartition
Other requirements were :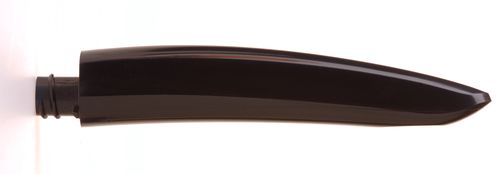
ADOP France manufactures a 32 cavity IBM mold
ADOP France is continuously meeting customer’s demands as their production requirements increase!
We met the challenge on a pharmaceutical project where the customer’s annual volumes required us to manufacture a 32 cavity mold ; our highest cavitation yet in IBM technology producing at unbeatable cycle times.
Chanel Hand cream bottle awarded 1st prize at the PCD 2018
This CHANEL product was the winner in the 2018 PCD Paris awards in the « premium skin care » category. One of the difficulties we faced as the mold maker of this product in IBM technology was to overcome the ‘theoretical infeasibility’ around the neck area. Other requirements that ADOP France had to fulfill here was the perfection and invisibility of the injection point & split lines as well as a high quality gloss finish.Christian Dior "ULTIMEYES” mascara : ADOP France took the challenge!
ADOP France was challenged on a project by our customer to manufacture a mold that many of our competitors in IBM technology had declined.This mascara bottle in both PP & PA with its curved form & curved cores required precision calculations and engineering to ensure a balanced wall repartition
Other requirements were :
- Off center injection point & the requirement of the injection point to be completely invisible
- Off center neck
- Invisible Split line requirement
- High gloss polish finish
ADOP France manufactures a 32 cavity IBM mold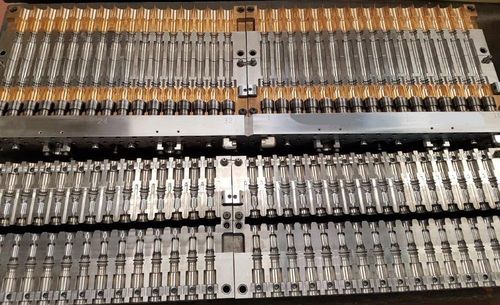
ADOP France is continuously meeting customer’s demands as their production requirements increase!We met the challenge on a pharmaceutical project where the customer’s annual volumes required us to manufacture a 32 cavity mold ; our highest cavitation yet in IBM technology producing at unbeatable cycle times.